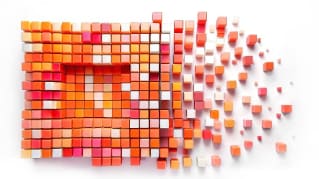
AI as a team member
AI opens up new possibilities for collaboration. But how can AI be integrated and trained as a team member, and how will it affect day-to-day work in agile teams?
AI opens up new possibilities for collaboration. But how can AI be integrated and trained as a team member, and how will it affect day-to-day work in agile teams?
Strategy& and PwC Autofacts® have analyzed electric vehicle sales worldwide in the first quarter of 2025.
Composable ERP equips ambitious businesses with the flexibility they need, but unlocking its potential demands navigating the common pitfalls.
Discover how the automotive industry is managing the shift to circular plastics.
Visit our careers website and discover the range of opportunities we have in our offices across Germany.
Find all PwC office locations by city across Germany and discover the office nearest to you.
We support journalists with industry research, facts, studies and direct access to our expert knowledge.
© 2017 - 2025 PwC. All rights reserved. PwC refers to the PwC network and/or one or more of its member firms, each of which is a separate legal entity. Please see www.pwc.com/structure for further details.